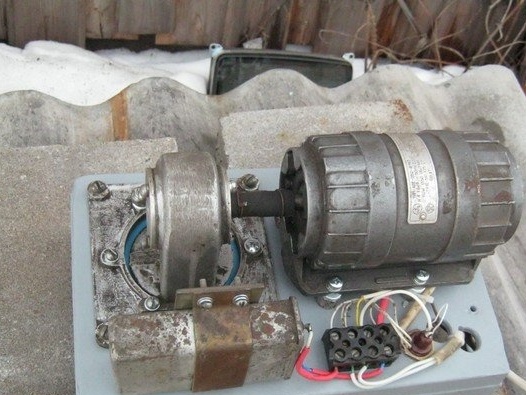
Il compressore d'aria KV-10 di piccola potenza e capacità mi è venuto in uno stato di riposo, dall'essere liberato dalla spazzatura il garage. Il compressore è stato prodotto nel 1981, l'era in cui il metallo non era risparmiato, ma qualsiasi attrezzatura civile richiedeva raffinamento e messa a punto.
Uno dei tubi dell'aria di rame (al pressostato) era attorcigliato e rotto nel compressore, una delle due valvole sul "cilindro principale" era rotta e tutte le parti in gomma - guarnizioni, membrane, gomma della valvola - erano indurite a morte. Inoltre, alcune parti sono state riempite con olio quasi vegetale, anch'esso polimerizzato dalla vecchiaia.
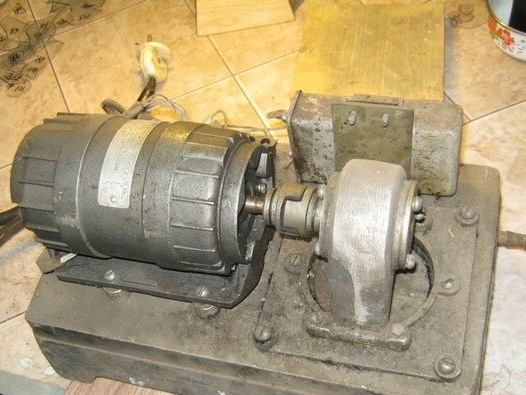
Un breve test ha dimostrato che il motore era in vita, pertanto sono stati intrapresi numerosi lavori per ripristinare il compressore.
Cosa è stato usato nel lavoro.
Tool.
Un set di piccoli strumenti da banco, un cacciavite (foratura), un saldatore da 40 W con accessori, un set di strumenti per l'installazione elettrica, un asciugacapelli per l'edilizia, un puzzle per gioielli sono stati utili. Per la pittura - pennelli, contenitori per materiali di verniciatura.
Materiali.
Cavo di alimentazione con spina, elementi di fissaggio, termotubo, interruttore a levetta affidabile, luce al neon. Tappetino in silicone, nastro FUM, LKM (incluso molto solvente - benzina, acetone, per lavare lo sporco), stracci.
Cosa è stato fatto

Il compressore non è facilmente smontabile. Elementi di fissaggio acidi e arrugginiti hanno superato con grasso penetrante un buon cacciavite e una piccola curva a piombo. L'olio e la gomma adesivi e induriti dovevano essere letteralmente raschiati con un coltello affilato e, se possibile, lavati via i residui con solventi.
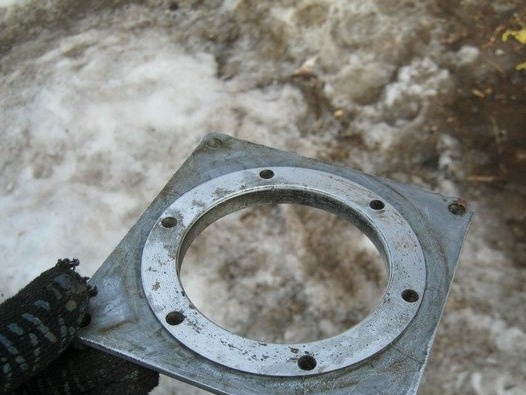
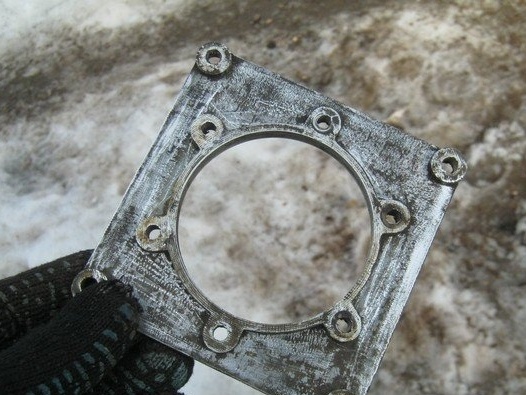
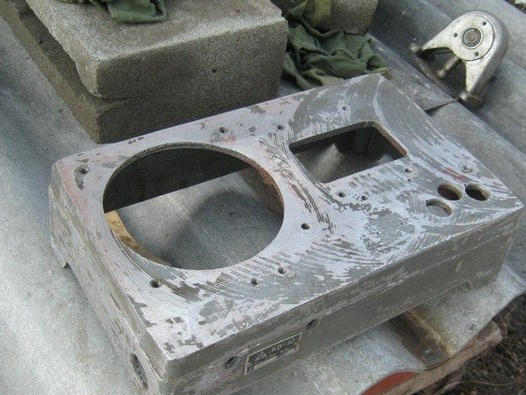
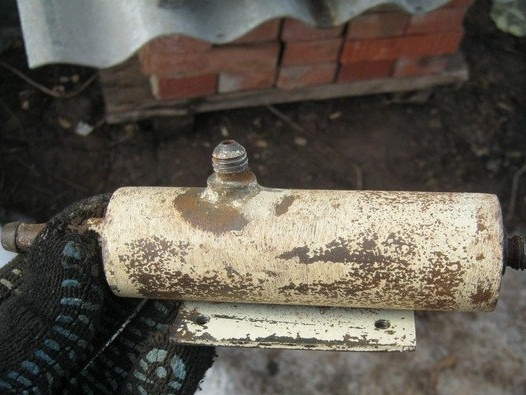
Il collettore in acciaio è stato accuratamente scosso dalla ruggine e soffiato, insieme a una base in alluminio, sgrassato con benzina e verniciato in due strati con smalto grigio. Il collezionista di ruggine esterna, la base per la bellezza.
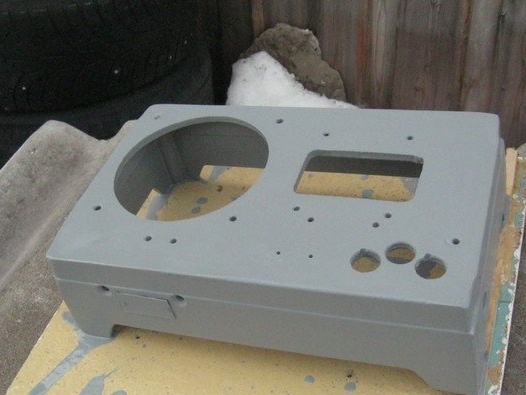
Pressostato
In generale, si è rivelato essere in buone condizioni. Dopo lo smontaggio, le parti interne e le parti vengono pulite con una pelle di medie dimensioni, spurgate e lavate con benzina. Invece della membrana indurita, la parte corrispondente è stata tagliata dal tappetino in silicone e gli elementi di fissaggio mancanti sono stati aggiunti durante il montaggio. Relè regolabile, progettato per una pressione molto bassa.
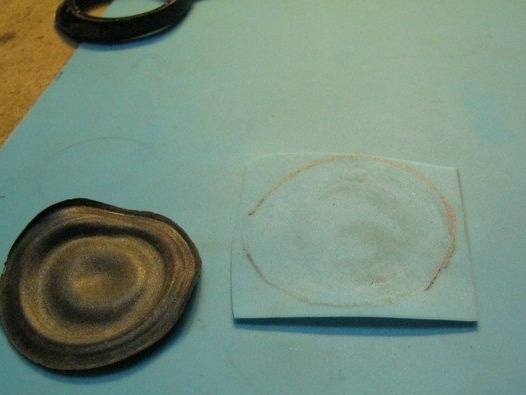
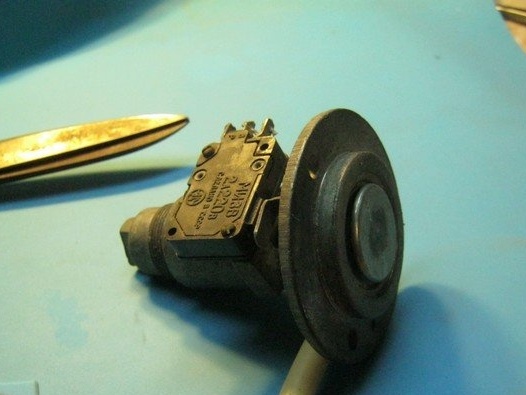
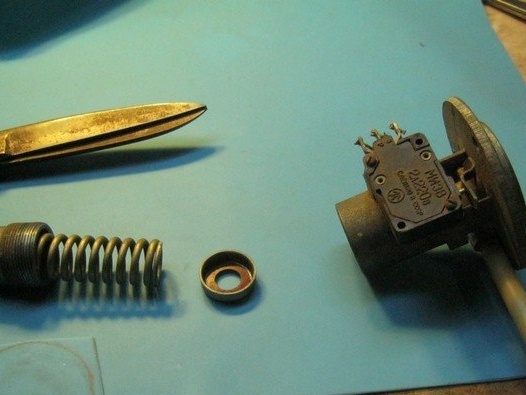
I componenti e le parti principali del compressore sono smontati il più possibile, puliti meccanicamente e solventi da sporco di olio grosso. Il grasso fresco viene riempito nei cuscinetti dell'albero motore e gli elementi di fissaggio mancanti vengono aggiunti al gruppo.Il motore era in buone condizioni, le condizioni dei suoi cuscinetti sono risultate soddisfacenti. Ha subito solo pulizie esterne.
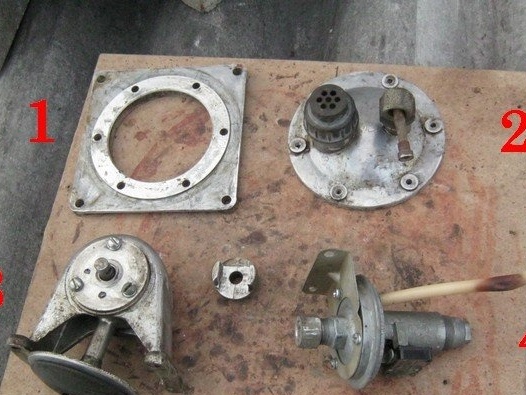
Valvola della pompa a membrana rotta.
Nel coperchio della pompa a membrana 2 (vedi foto sopra), oltre alle parti in gomma guaste, una delle valvole era rotta. Lo stop limitatore di textolite è stato lanciato nel volume di lavoro e rotto da uno spintore 3 (vedi foto sopra). Anche la cintura che limita la libertà di questa parte è spiegazzata.
Una parte spezzata simile era fatta di un pezzo di ottone. Il cerchio è segnato, i fori sono praticati, la parte è ritagliata con un puzzle di gioielli.
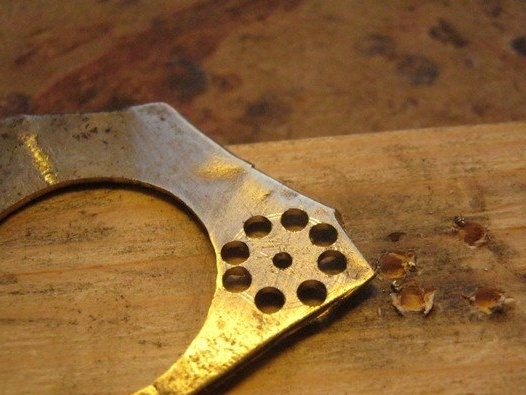
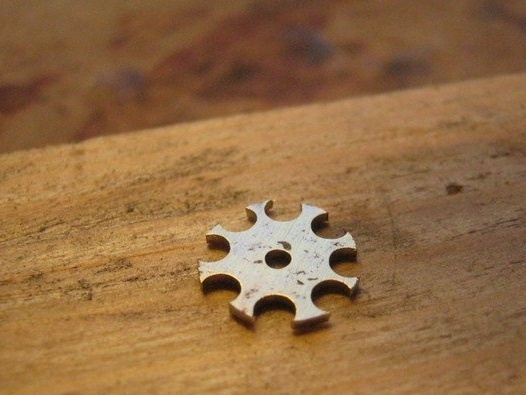
Il diametro della parte è regolato con un certo margine rispetto alla sede, la parte è ben levigata con una carta vetrata fine (contatto con un elastico) e martellata in posizione. Gli elastici delle valvole sono stati sostituiti con parti tagliate dallo stesso tappetino in silicone, gli elastici di tenuta induriti e incrinati sulle parti filettate delle valvole sono stati sostituiti con un nastro FUM.

Il diaframma della pompa è tagliato da un tappetino in silicone. Il morsetto a spinta è stato progettato per un grande spessore, in questo posto è stato posato un ulteriore strato.
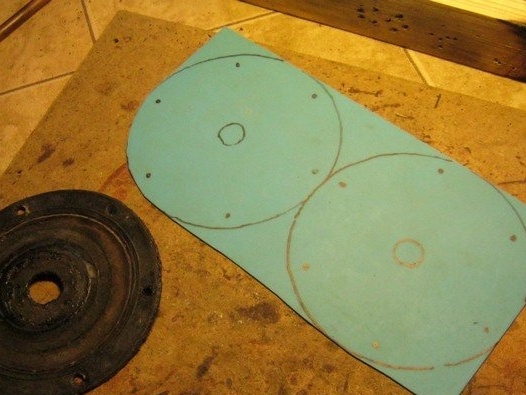
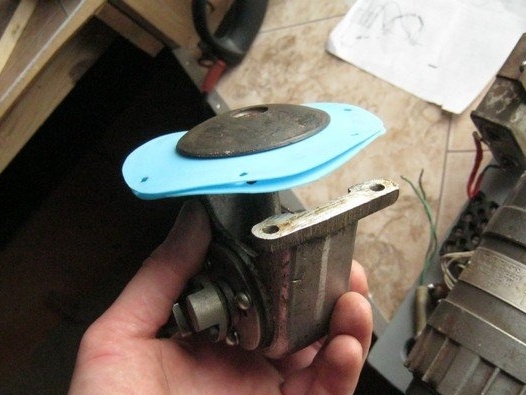
Inizialmente, ho provato a installare due strati della membrana, la versione finale con uno. Il secondo viene tagliato al diametro del supporto di plastica (cappuccio sul retro), altrimenti l'aria passa in questo punto.
Gruppo compressore
Su una base verniciata, un motore è montato sui rack, una base flangiata della pompa a membrana, una morsettiera, un condensatore del motore, un pressostato e un collettore d'aria (in basso).
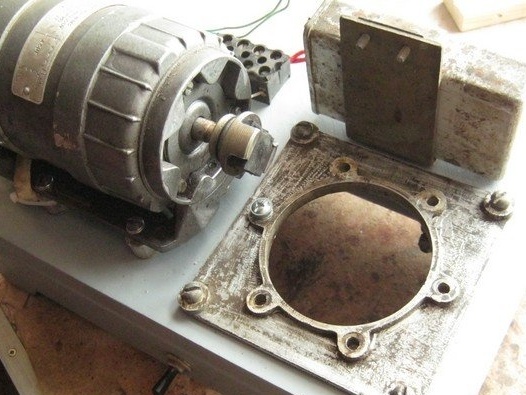
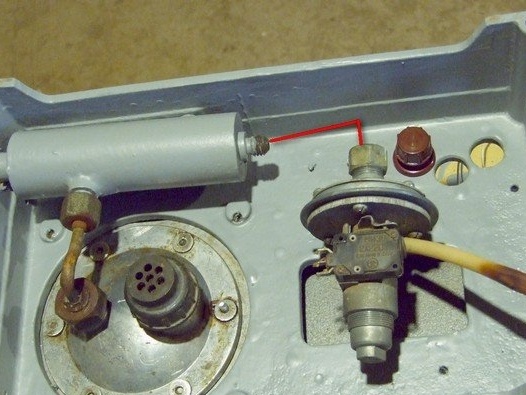
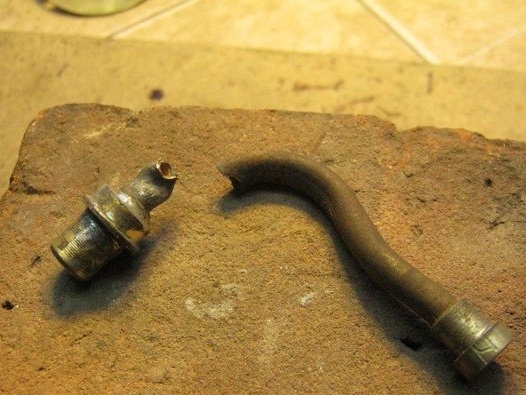
Sostituito il collettore pressostato del tubo di ottone rotto. Eyeliner rigido smontato, punte rimosse (una saldata) e pulite. È stato selezionato un tubo di rame di diametro vicino, è stato tagliato un pezzo adatto, le sue estremità sono state montate sulle punte. Bruciò il tubo con una torcia a gas, lo pulì e saldò una delle estremità. Ha modellato il tubo e sigillato la seconda estremità - montato e svasato nella seconda punta.
Il gruppo pompa a membrana (senza motore) presentava una resistenza piccola ma evidente nel punto inferiore della corsa dello spintore. Regolando l'altezza di installazione dello spintore sopra la membrana (posando le guarnizioni sotto la base del gruppo), è stato possibile ottenere una corsa uniforme della pompa completamente facile. Ho usato rondelle rinforzate (corpo) come guarnizioni.
L'accoppiamento sugli alberi della pompa e del suo motore era piuttosto rotto - inizialmente uno scarso allineamento e una scarsa lavorazione dei bordi del giunto mangiavano gomma e iniziavano a rompere le parti metalliche. L'accoppiamento è stato completamente rimosso, l'albero motore è stato accuratamente allineato con l'albero di carico mediante guarnizioni sotto la base del motore, gli alberi sono collegati da un pezzo di un tubo rigido (gas, per il cablaggio morbido da cilindri domestici con propano) con una benda di filo.
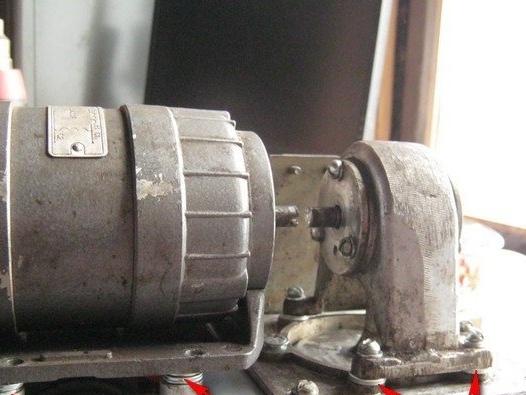
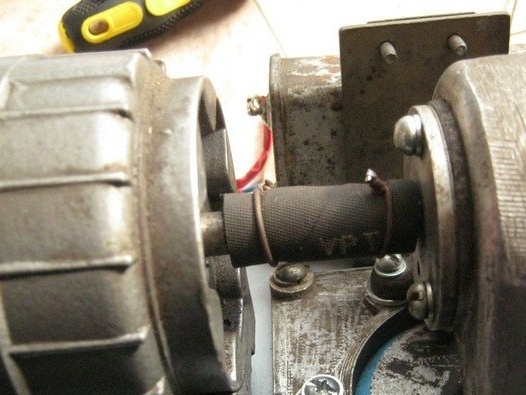
I test hanno mostrato le prestazioni complete della sostituzione: la forza trasmessa, grazie all'impostazione, è piccola, quando la linea dell'aria è bloccata, il pressostato interviene, spegnendo il motore.
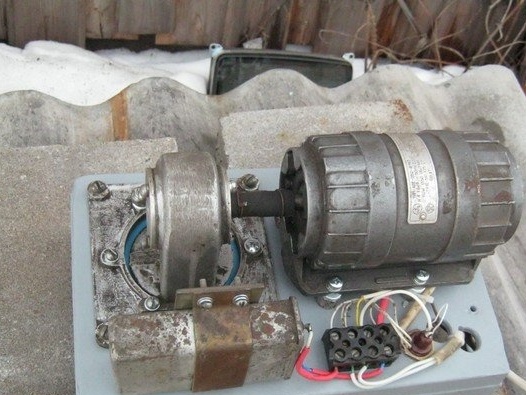
I collegamenti elettrici sono stati ripristinati, per comodità di funzionamento, è stato installato un interruttore a levetta nel compressore, che includeva l'alimentazione e una lampadina al neon con una resistenza di limitazione della corrente. La seconda spia per indicare il funzionamento del relè era ridondante. Il compressore non funziona silenziosamente, può essere ascoltato bene - è silenzioso ma la luce è accesa - il pressostato è scattato.
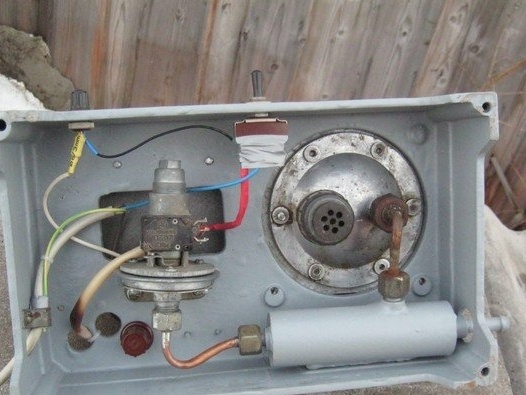
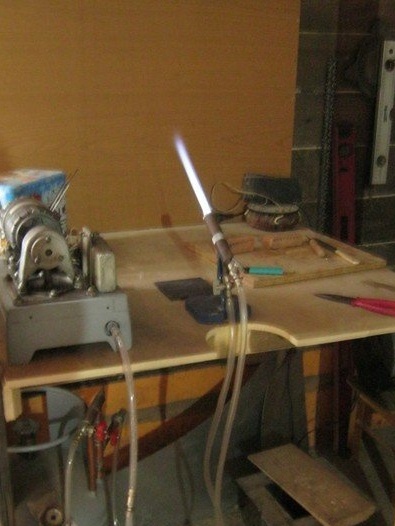
Il compressore è stato testato su un piccolo bruciatore di vetro con vapore di benzina. Sotto il tavolo puoi vedere carburatore a benzina.
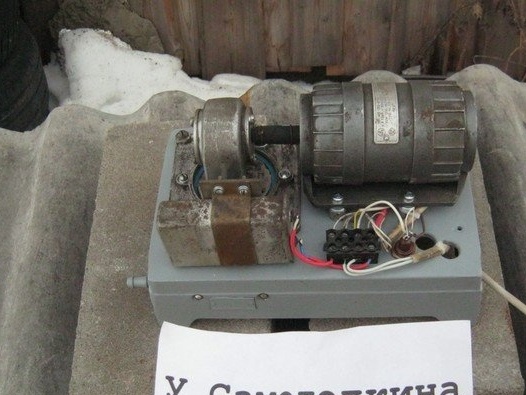
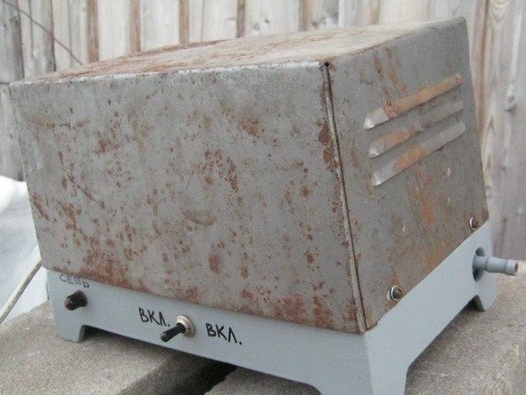
Conclusioni, modi per migliorare.
Tutti i lavori di restauro dell'unità miravano a sostituire il rumore compressore di costruzione per lavorare con i vapori di benzina. Il restauro, tuttavia, non è stato così silenzioso, soprattutto considerando il suo lavoro quasi costante. L'involucro del rumore del dispositivo riduce leggermente il rumore. In generale, per un funzionamento silenzioso a lungo termine (con vetro sul bruciatore), è possibile riconoscere il compressore come non idoneo, a meno che non venga rimosso dalla stanza. Tale dispositivo può essere raccomandato per bruciatori a vapore simili a benzina - per brasatura, ottone. Qui, il funzionamento del dispositivo sarà a breve termine e il suo rombo non diventerà un ostacolo speciale.
Durante il funzionamento della pompa a membrana, l'aria entra nel carico in porzioni; quando si lavora con il bruciatore, questo si manifesta come una piccola pulsazione della torcia.Lo svantaggio viene eliminato aggiungendo al dispositivo un ricevitore con una capacità di almeno alcuni litri. Con una pressione così bassa, può essere una bottiglia di plastica, una macchina fotografica per auto o diversi palloncini nidificati l'uno nell'altro per forza e inseriti in un sacchetto di stoffa.
Babay Mazay, marzo 2019