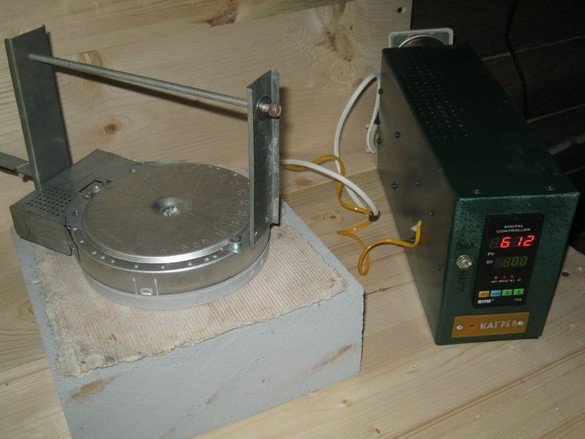
La fusione (eng. Fusione dalla fusione - sinterizzazione, fusione) è relativamente nuova cucito e com'è oggi, è nato nel 1990. Apparentemente, la fabbricazione di una vetrata "sinterizzata" è diventata possibile con l'avvento delle vetrate con uguale KTP (coefficiente di dilatazione termica). È fatto in questo modo: su una base di vetro, è disposto un modello di pezzi di vetro colorati e i loro bordi, nella maggior parte dei casi, non richiedono una regolazione e una lavorazione precise, un taglio sufficiente del vetro e tronchesi speciali. La preforma assemblata viene posizionata in un forno speciale e riscaldata alla temperatura alla quale il vetro si scioglie.
La vetrata che ne risulta appare molto particolare: bordi arrotondati e lisci, ogni elemento ricorda una sorta di caramella fusa. Con un po 'di abilità artistica, otteniamo gizmos molto interessanti. Inoltre, qui puoi applicare un intero arsenale di tecniche - usa fogli di metallo, segatura, filo, stampini per loro, tecniche di smalto cloisonné, applica vernici per cottura su vetro e ceramica, sostanze chimiche che danno bolle all'interno del vetro. Il forno di fusione consente anche lo stampaggio del vetro piano - la piegatura. Le aggeggi finiti possono essere combinati con metodi a "bassa temperatura", in grandi vetrate. In una parola: un abisso di opportunità per la creatività.
I vetri colorati, con lo stesso CTE, come molti materiali per la fusione, sono costosi, tuttavia l'articolo più costoso per padroneggiare questa tecnica è, ovviamente, la fornace. Una fornace per fondere gli occhiali è piuttosto insolita, la sua forma è dettata dalla tecnologia di sinterizzazione: un tavolo piano, sul quale è conveniente appoggiare un foglio di vetro bianco, un coperchio incernierato con riscaldatori. In generale, assomiglia a una valigia, su alcuni ci sono persino elementi di fissaggio.
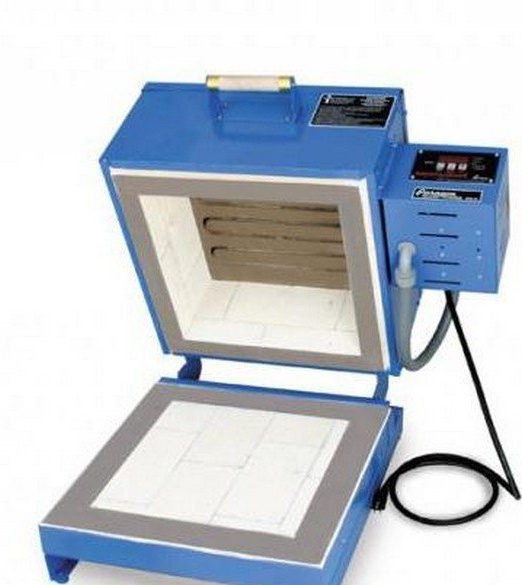
I forni a muffola - con un riscaldatore sopra la camera della muffola, non vengono utilizzati - dopo aver riscaldato il vetro fino al punto di fusione, il prodotto dovrebbe essere raffreddato abbastanza rapidamente alla temperatura di ricottura, mentre i forni sono spesso leggermente aperti. Un rapido calo di temperatura nella muffola è difficile: l'inerzia termica è troppo elevata ed è scomodo posare gli spazi vuoti nella camera.
Forni per la fusione, ci sono dimensioni molto diverse, rispettivamente - capacità. Con i riscaldatori di una piccola stufa, il cablaggio domestico può farcela molto bene.
Sinterizzazione del vetro "per non costoso".
Puoi provare te stesso in questo interessante business senza spendere ingenti somme - per cominciare, esiste una versione originale con Ali Express - crogioli speciali per il microonde. È un crogiolo refrattario con rivestimento in grafite all'interno. Il rivestimento viene riscaldato con onde a microonde e riscalda il vetro con radiazioni. C'è una virtù, ma un giusto importo - costo. Al momento della scrittura, il crogiolo costava 2-4 mila rubli. a seconda delle dimensioni.
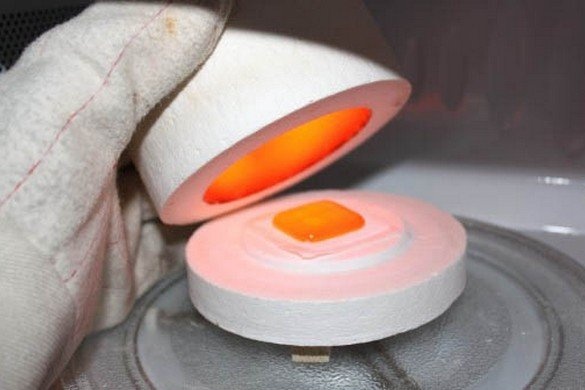
Gli svantaggi di un'opzione così semplice, come al solito, sono la massa. La temperatura può essere controllata solo visivamente, "ad occhio", impossibile ricottura controllata per alleviare le sollecitazioni interne. Di piccole dimensioni - solo per gioielli, l'incapacità di usare i metalli. Di norma, dopo aver selezionato sperimentalmente la modalità di sinterizzazione e aver consumato i frammenti di vetro inclusi nel kit, vengono lanciati l'occupazione e il crogiolo.
Un forno elettrico specializzato, ovviamente, è molto più perfetto, tuttavia, il più piccolo - 200x200 mm, costa 35 mila rubli. È chiaro - solo refrattari, un controller con profilo termico, tubi in quarzo e in ceramica per riscaldatori, di nuovo assemblaggio ... Avendo un'officina o un garage, un po 'di abilità nella lavorazione dei metalli ed esperienza con l'elettricità, è abbastanza possibile assemblare un tale forno da soli, spendendo meno della metà del costo dei materiali , ma cosa fare residenti senza cavallo e senza garza della "giungla di cemento"?
Idea.
L'idea di un forno di fusione estremamente semplice ed economico con caratteristiche “intermedie” appartiene Il compagno. "Ilya MSU", dal forum metal. Il forno è di piccole dimensioni, ma è già possibile cuocere il vetro, molto più serio dei ciondoli con spilla ad anello nel forno a microonde. Puoi usare filo, lamina e l'intero arsenale di tecniche di fusione. Resistenza elettrica a resistenza nel coperchio, termocoppia con un semplice termoregolatore. Bassa, anche per una potenza dell'appartamento, la capacità di produrre in cucina da parti poco costose, elementi. Il design non contiene refrattari specializzati ad alta temperatura.
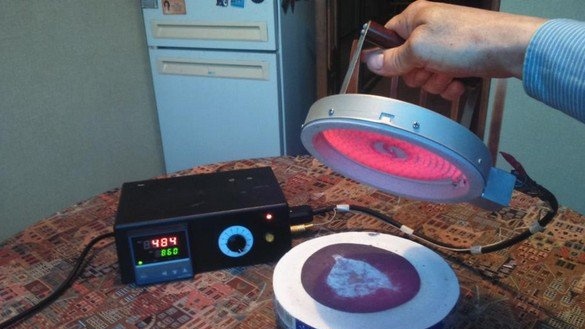
Come copertura superiore del forno della valigia, viene utilizzata una parte di una stufa elettrica con una superficie in vetroceramica: un bruciatore. Ha un involucro metallico rivestito con refrattario fibroso, in cui si formano speciali sporgenze del nastro riscaldante. Il bruciatore è completato da una maniglia e una termocoppia collegate a un semplice controller. Come base, è stata utilizzata una lattina piatta riempita di intonaco.
Versione propria di una semplice stufa a bruciatore.
Ho avuto due bruciatori di seconda mano con un diametro "funzionante" interno di 140 mm, con un termostato meccanico in una cassa di metallo (ci sono opzioni con un tubo al quarzo).
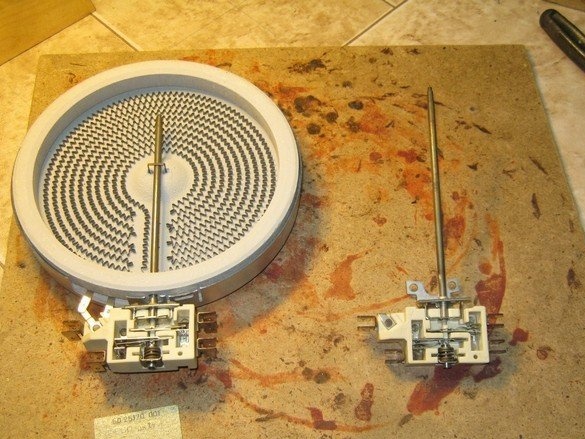
Ciò che è stato utilizzato al lavoro.
Strumenti, dispositivi, attrezzature.
Una serie di normali strumenti da banco di medie dimensioni, un puzzle per gioielli con accessori, una smerigliatrice angolare piccola, un cacciavite o un trapano elettrico. Un set di strumenti di cablaggio, un saldatore da 40 W per il cablaggio, più grande - 60 ... 80 W - per la saldatura strutturale. Strumento di marcatura. Strumento utile per l'installazione di rivetti ciechi, la costruzione di asciugacapelli.
Materiali.
Oltre ai bruciatori stessi, avevano bisogno di fogli di amianto, mattoni di cemento espanso, fili diversi, una termocoppia, termotubi, fascette in nylon. È stata utilizzata un'unità di controllo pronta per un forno a muffola (o un controller + relè a stato solido + radiatore + custodia). Resistenza di estinzione di potenza adeguata (riscaldatore olio). Un po 'di elementi di fissaggio in acciaio zincato.
I contatti del termostato del bruciatore sono stati forzatamente chiusi e saldati, saldatura di stagno-rame ai terminali di uscita, fili di isolamento in silicone sono stati saldati. Accanto al termostato, è stato praticato un foro nella cavità interna, è stata introdotta una termocoppia cromel-alumel (tipo K), da un multimetro. Alla sonda del termostato standard, la termocoppia ha attaccato diversi giri di filo di nicromo.
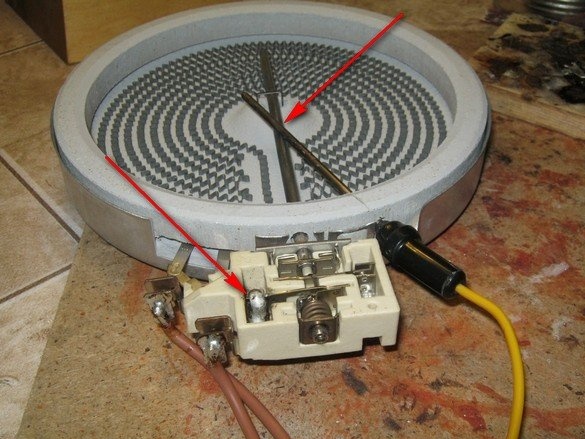
Copertura di latta - in effetti, si è rivelato essere l'elemento più difficile della mia fornace. È saldato dall'acciaio zincato “tetto” 0,5 mm, saldatura stagno-rame (il punto di fusione è superiore a quello delle saldature al piombo). Flusso - acido di saldatura (cloruro di zinco), saldatore 60 watt.Parti complesse sono state segate con un puzzle di gioielli, tagli dritti - con forbici di metallo. Le linee curve erano contrassegnate in questo modo: il pezzo di ferro veniva messo nel posto giusto e con un paio di bussole, con un ago al centro del bruciatore, disegnavo il raggio necessario per l'arco.


Saldato dall'interno, principalmente per l'estetica. Di fronte ai terminali a "coltello" del termostato standard del bruciatore, con fili saldati su di essi, si creavano dei fori di ventilazione (sopra e sotto) sull'involucro in modo che fossero raffreddati da una corrente d'aria e la saldatura non si sciogliesse.
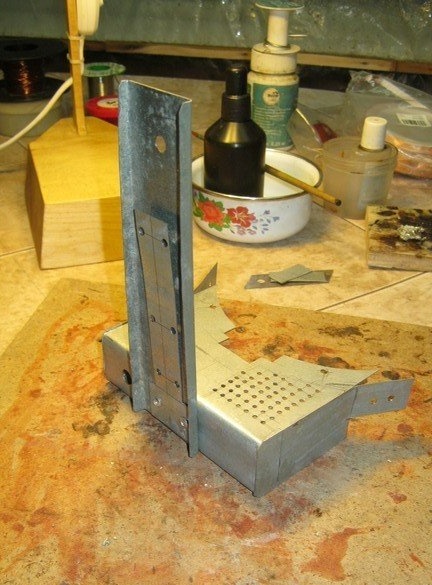
Oltre il bordo dell'involucro, ho deciso di agganciare e una delle staffe per l'impugnatura, con gli stessi elementi di fissaggio, ha bloccato un supporto per i fili. Pezzi di latta fissati con rivetti ciechi in alluminio.
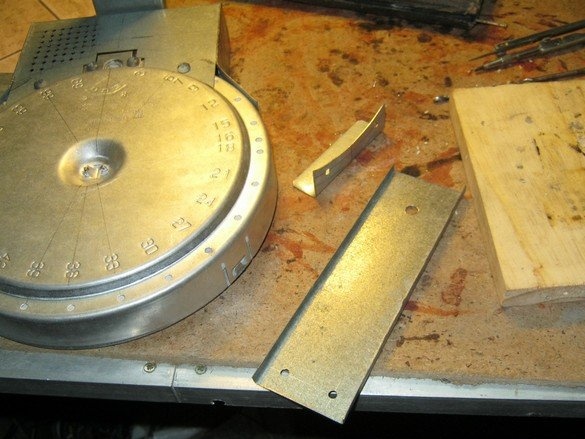
La staffa anteriore per la maniglia era montata su un involucro normale ed è composta da due parti di stagno. È fissato all'alloggiamento con viti autofilettanti corte, il collegamento tra loro è rivettato.
La parte esterna.
Il riscaldatore del bruciatore, con una potenza di 1200 W, è troppo potente per i bicchieri di cottura: la velocità di riscaldamento è ottima per un volume così piccolo, il vetro non ha il tempo di riscaldarsi uniformemente, il pezzo si incrina. Per eliminare l'inconveniente, è stato necessario ridurre la potenza del riscaldatore - per attivare una potente resistenza in serie con esso - un riscaldatore ad olio a metà potenza. Allo stesso tempo, sul riscaldatore del bruciatore, la caduta di tensione è esattamente la metà della tensione di rete - 110 volt.
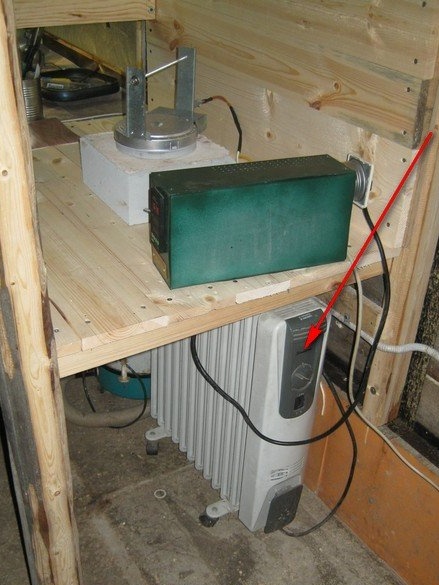
Controller per il controllo del forno. Sulla sua parete posteriore sono montati una presa per il collegamento e una morsettiera a vite per il riscaldamento del forno. La termocoppia è collegata direttamente al controller.
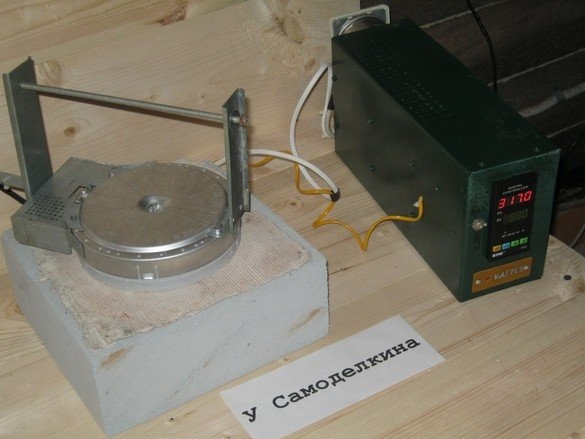
Il coperchio del forno è su base refrattaria - foglio di amianto, sotto il quale la metà del mattone è realizzata in calcestruzzo espanso. Nelle vicinanze, vale la pena mantenere lo stesso rivestimento resistente al fuoco - su di esso, se necessario, puoi mettere la punta calda della fornace "aperta".
Sinterizzazione.
Quando si sinterizzano i vetri, è necessario mantenere due temperature principali: l'inizio della fusione del vetro (710 ... 800 ° C a seconda del tipo di vetro) e la temperatura di ricottura (500 ... 600 ° C a seconda del tipo e delle dimensioni del pezzo). Il riscaldamento iniziale avviene il più agevolmente possibile (entro limiti ragionevoli, ovviamente), dopodiché la temperatura scende rapidamente a "ricottura".
In genere, il processo è controllato da un controller programmabile "con profilo termico". Qui viene applicato un semplice controller, mantenendo una temperatura, e vengono commutati, manualmente - un dispositivo semiautomatico. Al raggiungimento di 800 ° C (~ 30 min.), Il coperchio del forno è socchiuso, sul controller viene impostato 500 ° C e il prodotto viene ricotto per 1 ora. Successivamente, i riscaldatori del forno vengono spenti e il prodotto si raffredda con il forno a temperatura ambiente (~ 1 ora). Le piccole dimensioni del vetro consentono di non temere piccole imprecisioni nel processo.
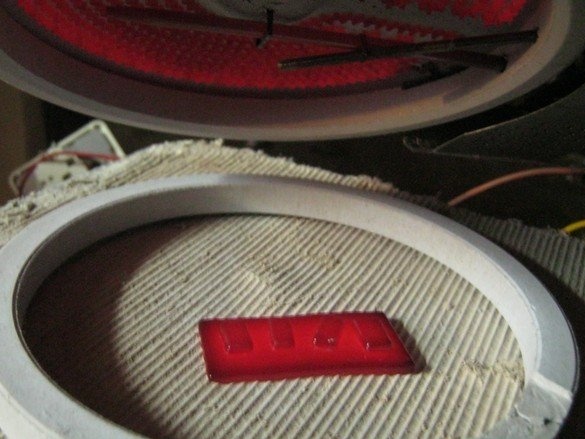
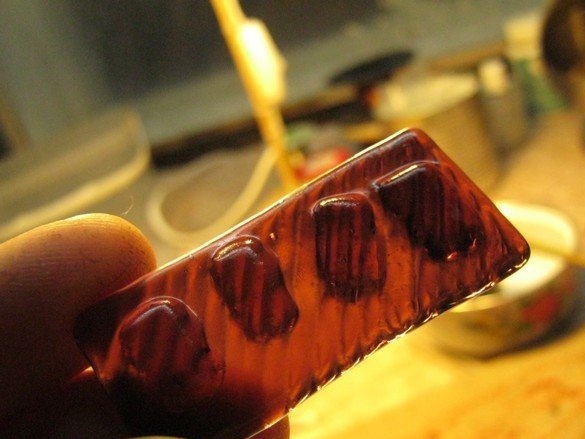
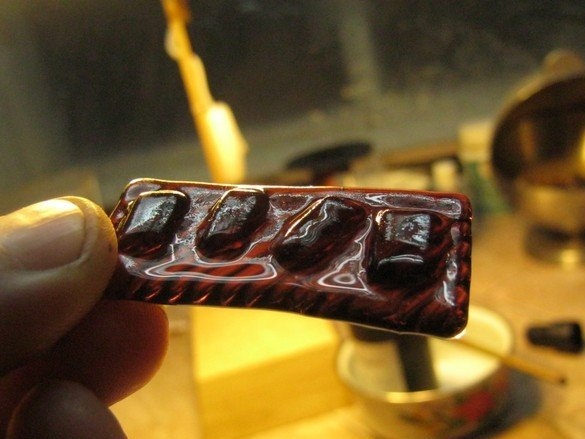
Bene, il primo esperimento ha abbastanza successo - gli occhiali si sono fusi, ma non su una superficie piana, il campione non si è rotto - il profilo di temperatura per questo tipo di vetro dovrebbe essere considerato di successo. Cerchiamo di essere più significativi.

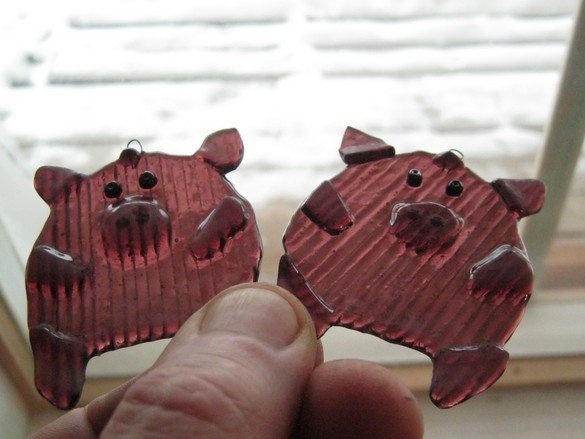

Due bestie, hmm, abbastanza nello spirito del giorno, come gli orsi olimpici, una volta ... Qui, come esperimento, due varietà di perline sono state fuse, filo di rame, il vetro è stato fuso non solo "grembo" ma anche praticamente "testa a testa". Le perle (vetro con un diverso KTP) e il filo di rame (tanto più) dovrebbero essere molto piccoli (diametro, sezione trasversale) rispetto al vetro principale, quindi le sollecitazioni risultanti non distruggeranno il prodotto.
Babay Mazay, dicembre 2018